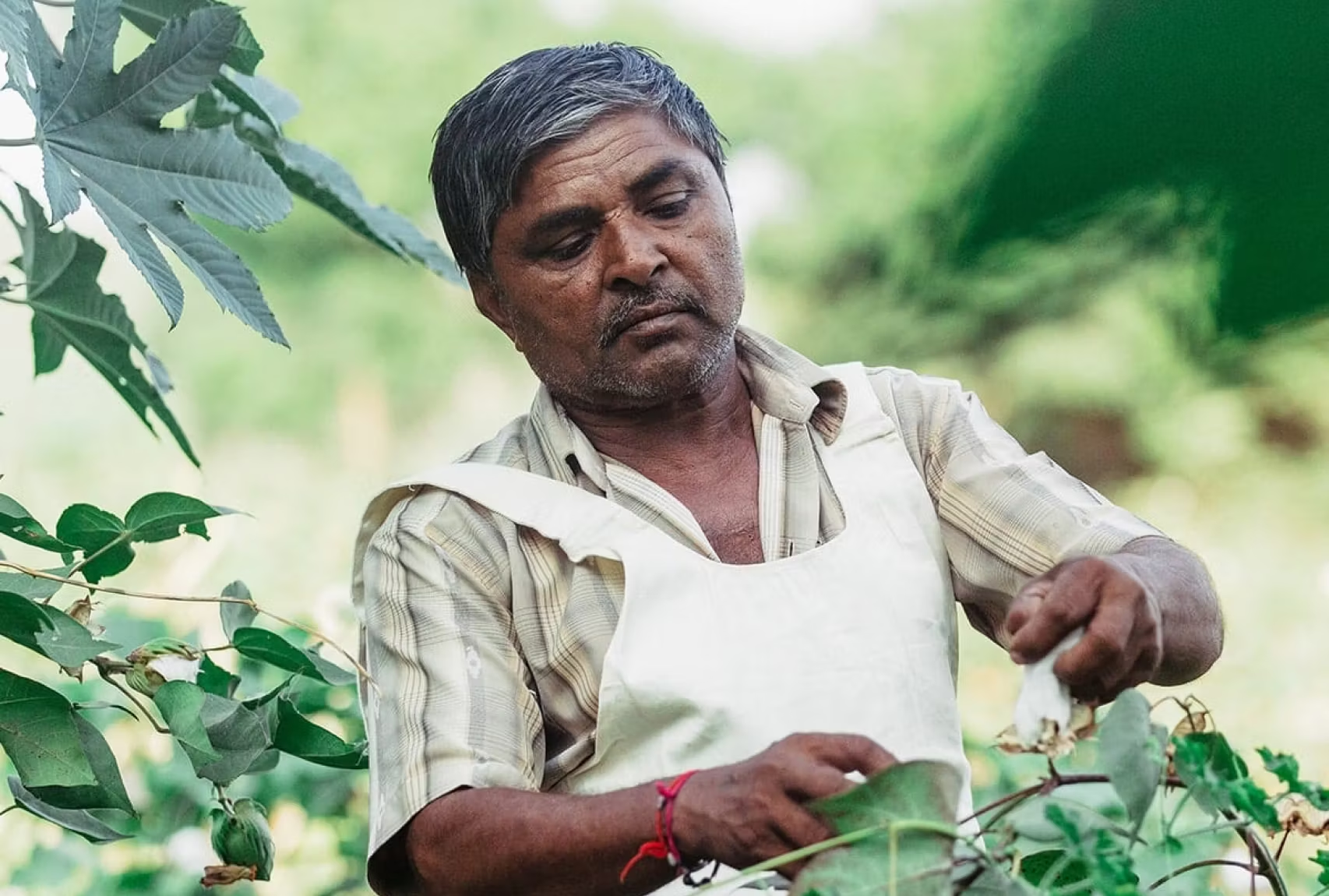
Step 1
Der Anbau
Unsere Bio-Baumwolle wird nach den Richtlinien des ökologischen Landbaus angebaut. Langzeitstudien über ökologische Betriebe haben gezeigt, dass der ökologische Landbau 18 Prozent weniger Treibhausgasemissionen verursacht als andere Anbausysteme.* *Quelle: Textile exchange (2021) Material summary on Organic, In-Conversion Cotton. .
Stattdessen düngen die Bäuer*innen mit Mist und Kompost, was die natürliche Fruchtbarkeit des Bodens und seine Erosionsresistenz zirkulär aufbaut. Ein jährlicher Fruchtwechsel ist ebenfalls vorgeschrieben. So wird durch den rotierenden Anbau der Baumwolle mit anderen Kulturen Schädlingen und Krankheiten natürlich vorgebeugt und der Boden weiter angereichert.
Durch seinen erhöhten Humusanteil ist der Boden nicht nur fruchtbarer: er kann zudem mehr Wasser und atmosphärisches CO2 speichern.
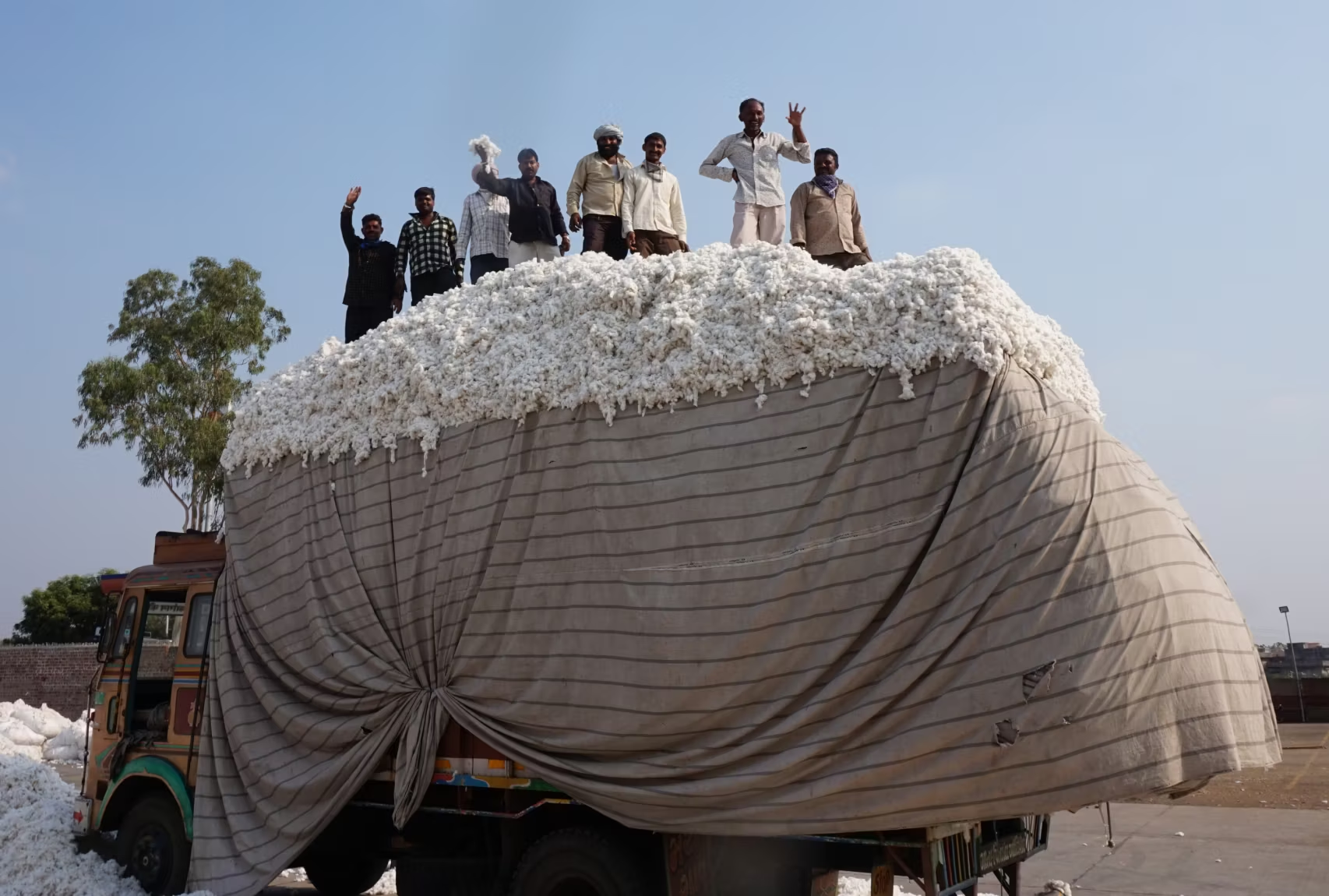
Step 2
Die Ernte
Bio-Baumwolle wird einmal jährlich geerntet. Anders als beim konventionellen Baumwollanbau sind chemische Entlaubungsmittel, die zur Erleichterung einer maschinellen Beerntung eingesetzt werden, verboten.
Um den Wechsel von konventioneller auf Bio-Baumwolle zu erleichtern, haben wir im April 2018 die ARMEDANGELS Organic Farmers Association gegründet. Diese unterstützt derzeit über 500 Kleinbäuer*innen in Indien beim dreijährigen Umstellungsprozess
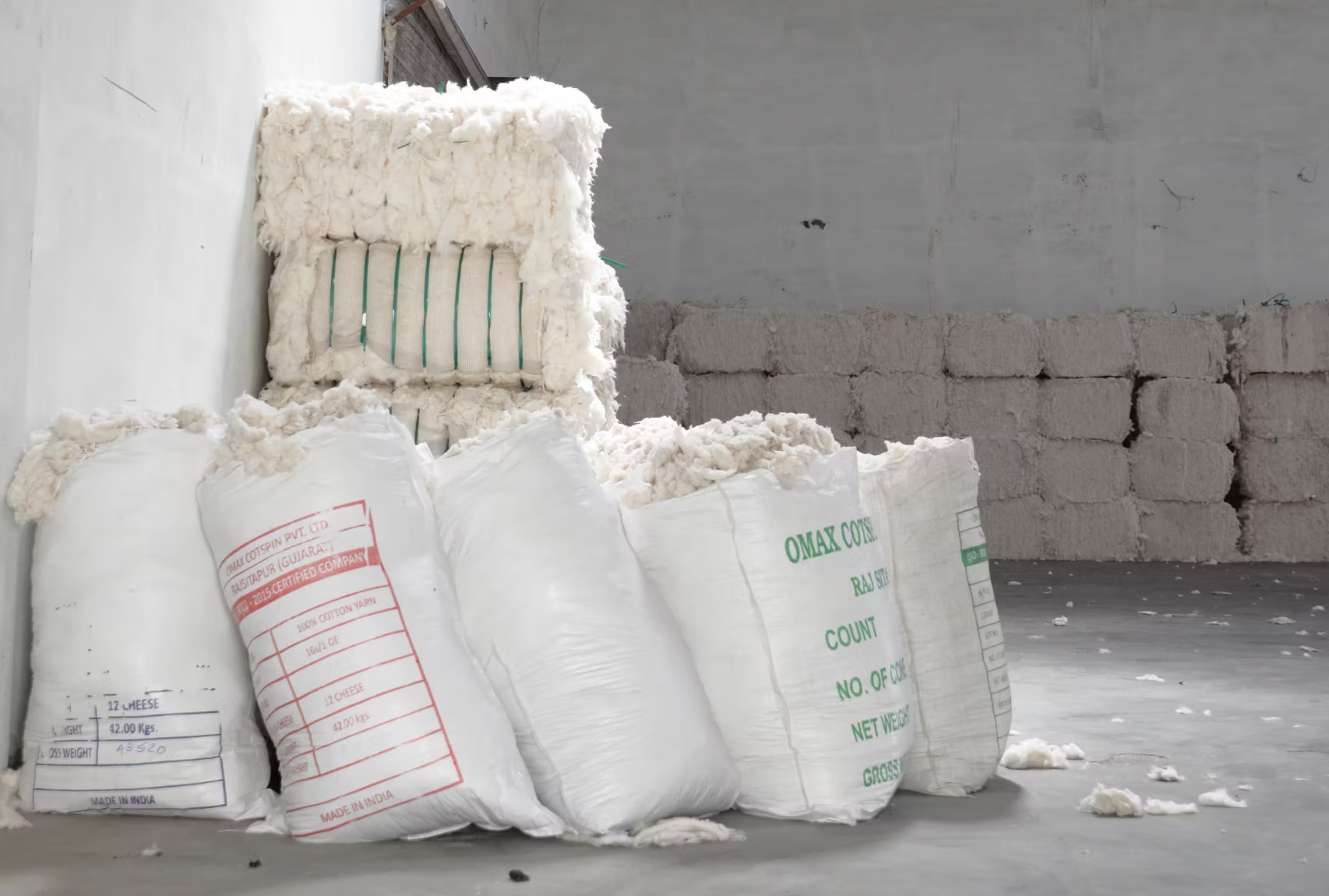
Step 3
Die Faser
Unmittelbar nach der Ernte wird die Rohbaumwolle in spezielle Verarbeitungsbetriebe gebracht, um die Baumwollfasern vom Samen zu trennen. Dies geschieht vollautomatisch mit Hilfe einer speziellen Entkörnungsmaschine, der Cotton-Gin.
Während der gesamten Entkörnung gelten strenge Kontrollen, um die Baumwolle nach Qualität und Anbaumethode (biologisch oder konventionell) getrennt zu halten.
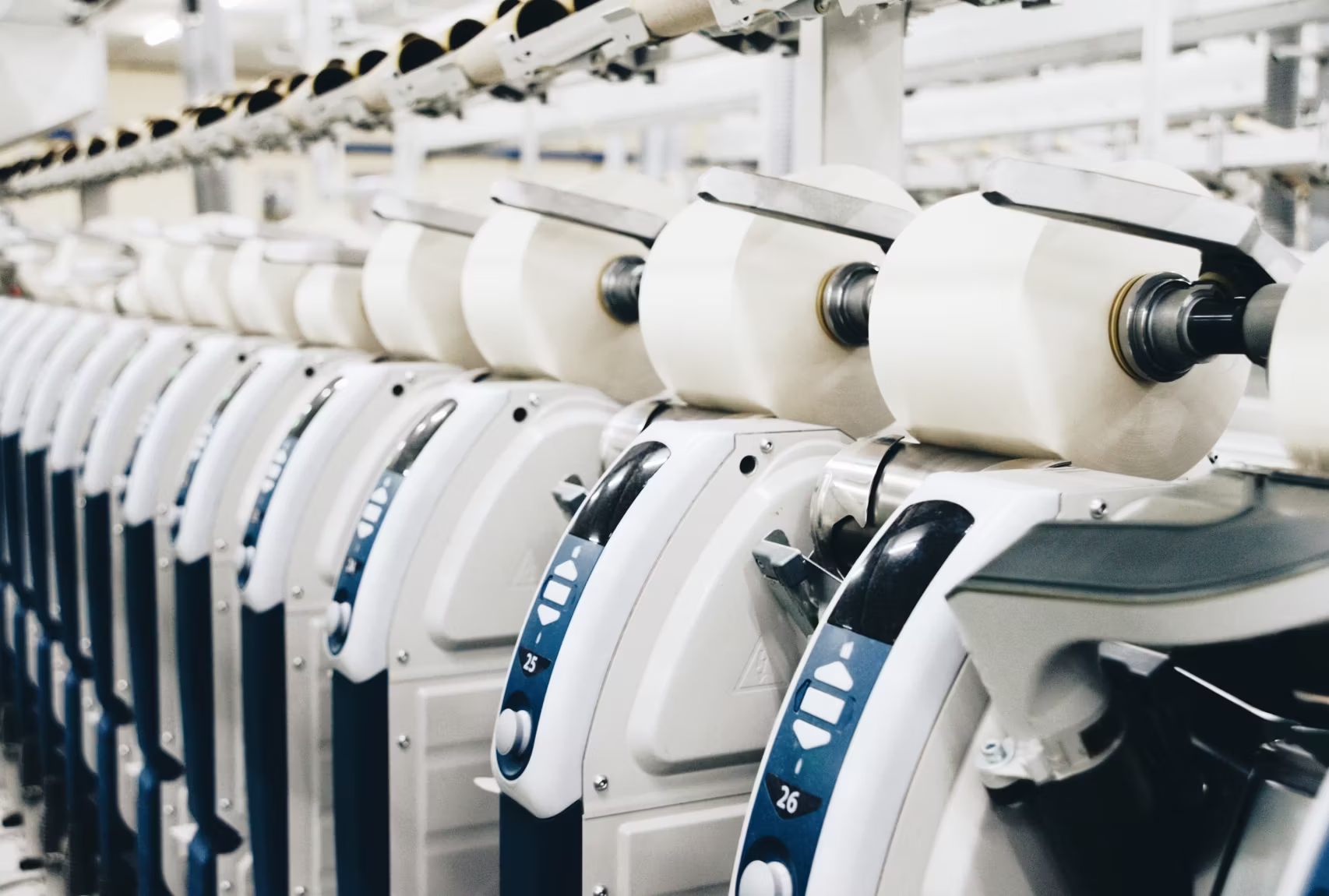
Step 4
Das Garn
Beim Spinnen werden einzelne kurze Fasern und Faserbündel durch Verziehen und Zusammendrehen zu einem gleichmäßigen Faden bzw. Garn zusammengebracht. Was früher noch ein mühevoller Prozess mit Hand und Spinnrad war, funktioniert heute vollautomatisch.
Der fertig gesponnene Faden wird abschließend und zur weiteren Verarbeitung zu Strängen oder auf Konen gewickelt.
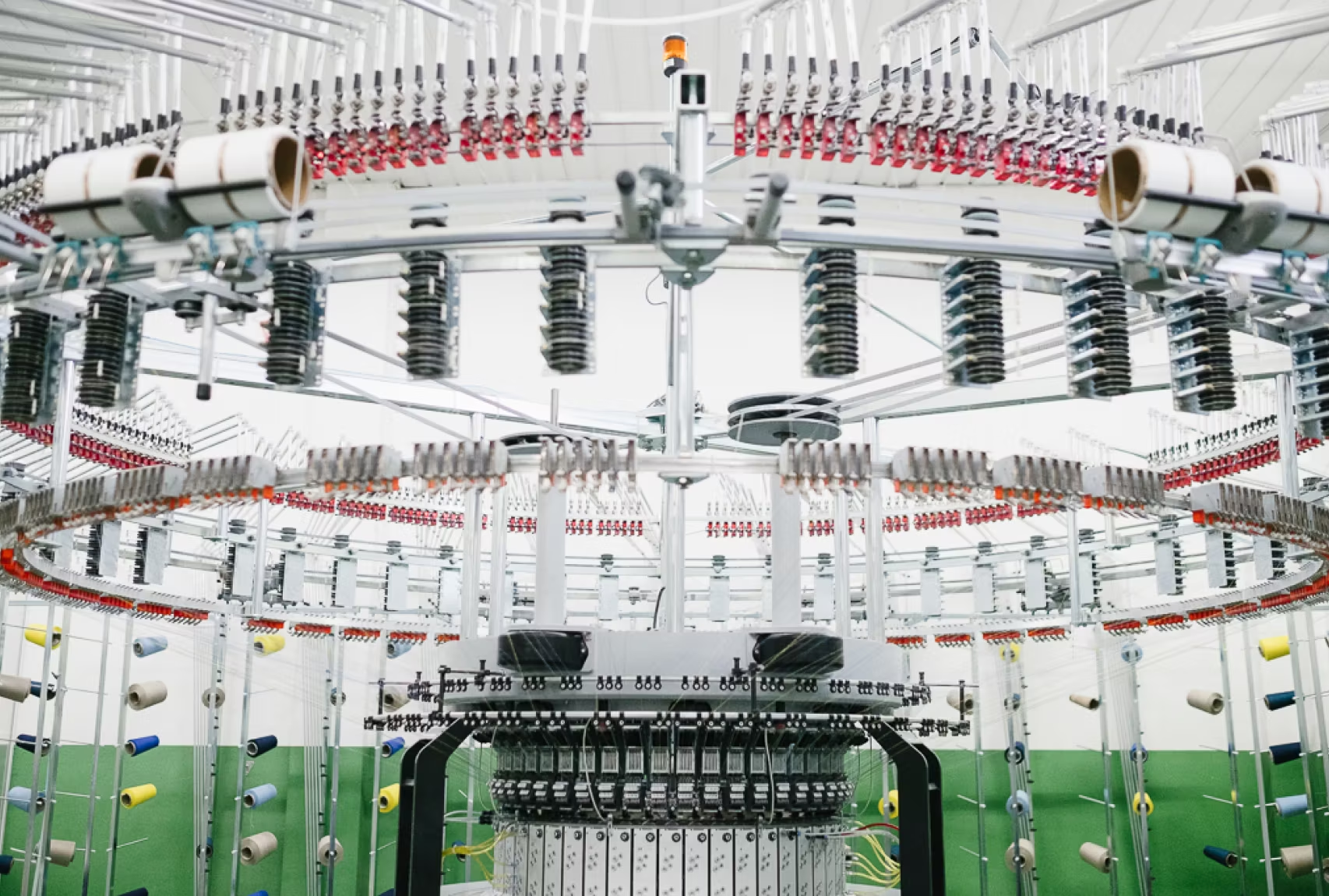
Step 5
Stricken
Für unsere T-Shirts aus Bio-Baumwolle wird ein Single Jersey Stoff hergestellt. Anders als Gewebe, bei denen zwei Fadensysteme verkreuzt werden, handelt es sich dabei um einen Maschenstoff, bei dem Fadenschleifen mit anderen Fadenschleifen verbunden werden.
Dieser Prozess geschieht vollautomatisch an großen Rundstrickmaschinen, die viele einzelne Garne zur textilen Jerseyfläche verstricken.
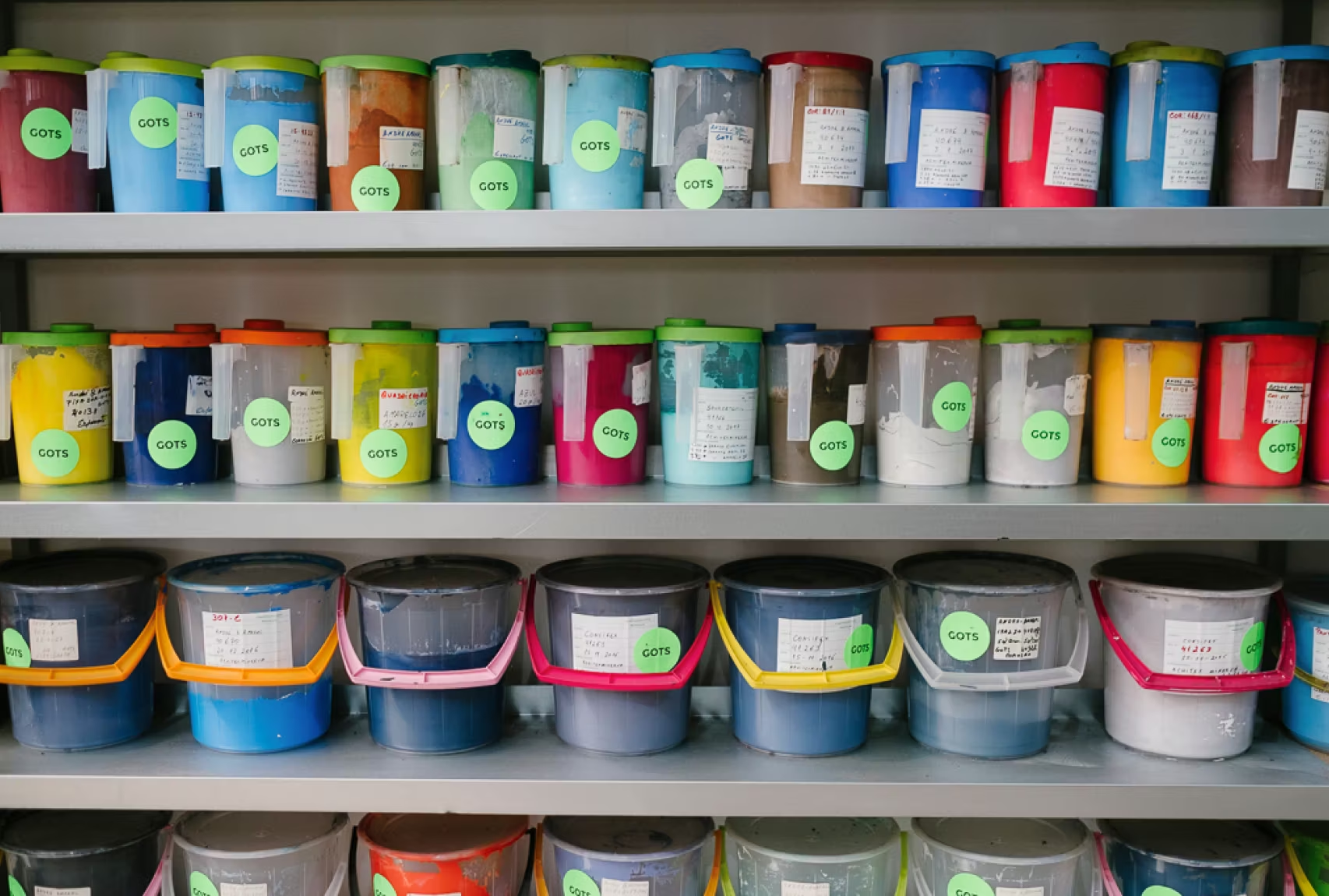
Step 6
Färben und veredeln
Je nach Textil erfolgt das Färben und Veredeln an unterschiedlichen Stellen im Produktionsprozess: beim Garn (Streifenstoffe), der textilen Fläche oder dem fertigen Kleidungsstück (Garment Dye).
Beim Färben von Textilien werden im konventionellen Bereich viele chemische Produkte eingesetzt und Gesundheitsrisiken in Kauf genommen. Enthaltene Schadstoffe können sich beim Tragen eines T-Shirts von der Faser lösen, in den Körper eindringen und allergische Reaktionen oder Krankheiten des Immunsystems hervorrufen.
Eine Alternative stellen Färbemittel dar, die unter dem Global Organic Textile Standard zugelassen sind. Alle Farben und chemischen Hilfsmittel sind darin toxikologisch geprüft. Durch moderne Filtrationssysteme wird auch das Abwasser nicht belastet.
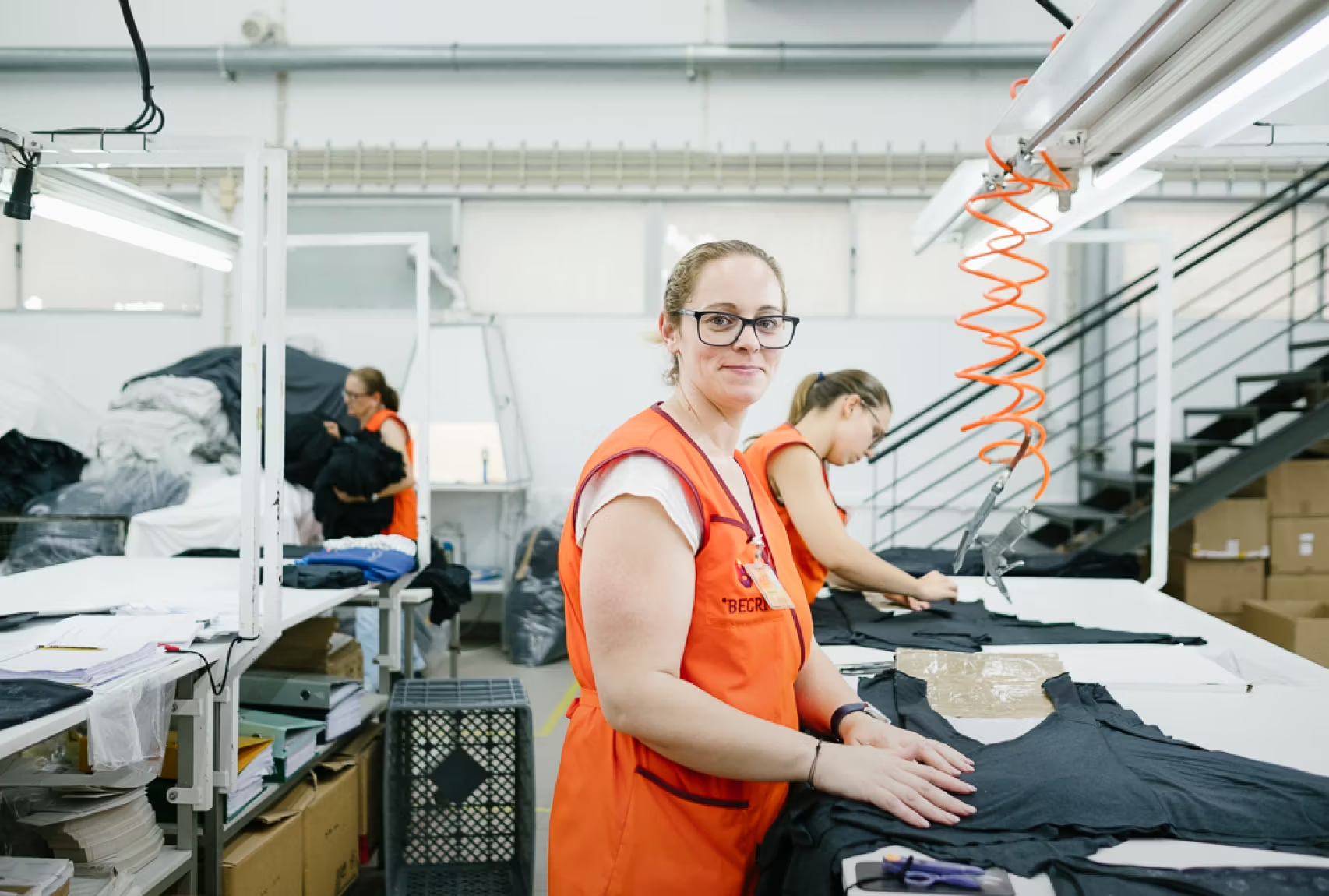
Step 7
Die Konfektion
Die Konfektion umfasst das Zuschneiden, Nähen und Finishen eines Kleidungsstücks. Hier wird aus der 2-dimensionalen textilen Fläche ein 3-dimensionales Kleidungsstück.
Die Konfektion für unser Bio-Baumwoll T-Shirt JAAMES findet in Portugal bei unseren zertifizierten Partnern statt. Wie bei allen Partnern bedingen wir hier: faire Löhne für die Arbeiter*innen in den Nähfabriken, keine Kinderarbeit, mehr Sicherheit am Arbeitsplatz und weniger Überstunden.